We are implementing a digital solution for the organization and inspection of cleaning for the food industry. It allows to improve the traceability of the cleaning quality as close as possible to the need (before, after or during production).
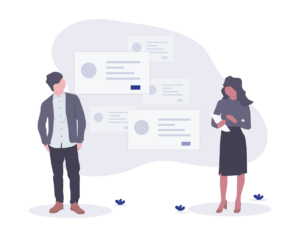
Requirements
- You have difficulties to optimize the time spent setting up a quality follow-up of the cleaning of your premises/equipment;
- You are looking to improve the follow-up of cleaning operations in order to set up or improve the quality controls of your production lines;
- You want to allow your teams (cleaning, production, quality) to communicate better with each other in order to be more responsive to anomalies detected during production or after cleaning;
- You want to be more efficient and responsive because a cleaning defect on equipment should have the least possible impact on the rest of the production chain;
- Your are looking for a solution to facilitate the implementation of a quality plan to track ALL these events;
We have THE solution!
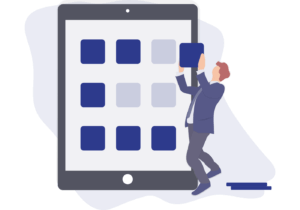
Answer
Our mobile solution makes it possible to simplify the quality follow-up of the various stages of the cleaning process of premises and agri-food equipment.
By determining a detailed cleaning plan targeting areas to be inspected (premises, production line, equipment…) our application helps to formalize and simplify cleaning operations (detergent, disinfectant, concentration rate, contact time, rinsing protocol,…)
A quality plan is also to be defined in order to list the different controls carried out by the quality team (Biofilms/ATP, microbiological by Rodac Agar, Listeria swabs…)
The cleaning plan can be modified at any stage of the process to meet a specific need such as increased cleaning after quality control that does not meet established standards.
Non-conformities are dealt with quickly and the required actions are forwarded to the appropriate teams.
The data collected during the controls thus provide optimum traceability of the cleaning and verification process.
A digital link booklet allows the transmission of incidents/remarks between the different teams (production, cleaning, quality service, sanitary inspectors) present at different times during the process.
The statistical results of bacteriological inspections can be viewed in a set of dashboards providing a centralized, near real-time view of all health inspection activities performed within your organization.
All the operations described above are accessible according to the rights granted to the user.
The cleaning plan is dynamically modifiable if a reinforced cleaning need is required.
Non-conformities are rapidly reported and the required actions are forwarded to the teams concerned.
The data collected and the test results provide optimum traceability.
A statistical database is generated, giving for each area, equipment and sub-equipment the results and interpretations of the bacteriological inspection data (final rating).
A dashboard provides a centralized, all most real-time view of all health control activities. It is accessible according to the rights granted.
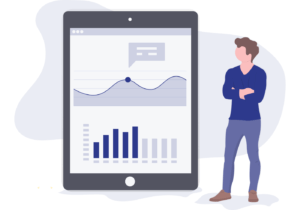
Benefits
- Traceability of the cleaning and verification process through the implementation of a digital data collection process.
- Improving communication between departments: cleaning, production and quality.
- The use of data in the short term (daily cleaning), medium term (evolution of the control plan) and long term (statistics).
- Better planning of cleaning steps. This also makes it possible to objectify cleaning and quality controls.
Illustration
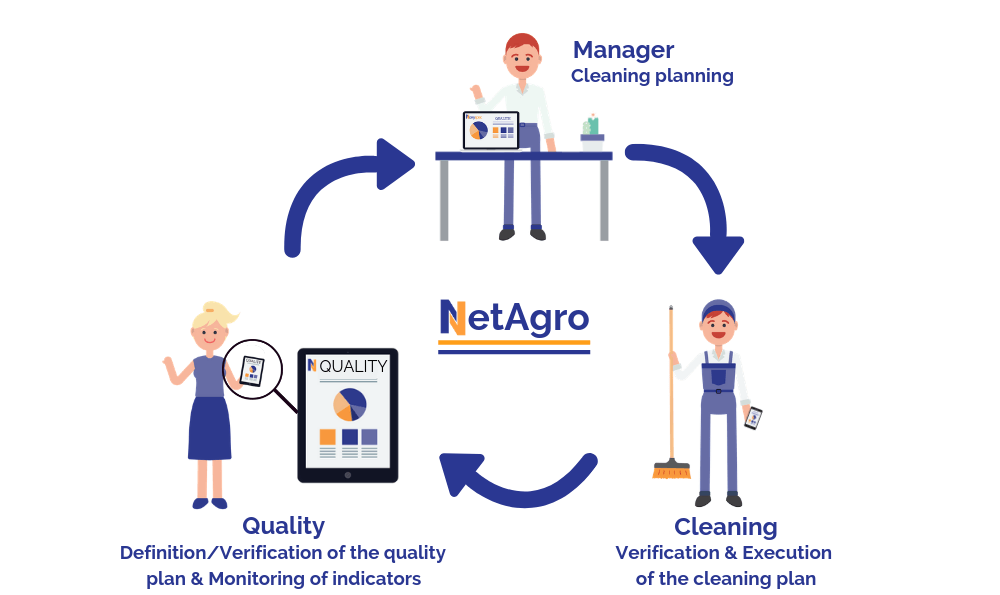